Engine oil filters are critical in safeguarding an engine’s health by removing contaminants, ensuring optimal engine performance, and prolonging vehicle life. Mass production of oil filters, however, poses unique challenges to manufacturers: maintaining quality, consistency, and efficiency at scale. Below, we outline key steps and best practices to produce engine oil filters on a large scale, without compromising on quality.
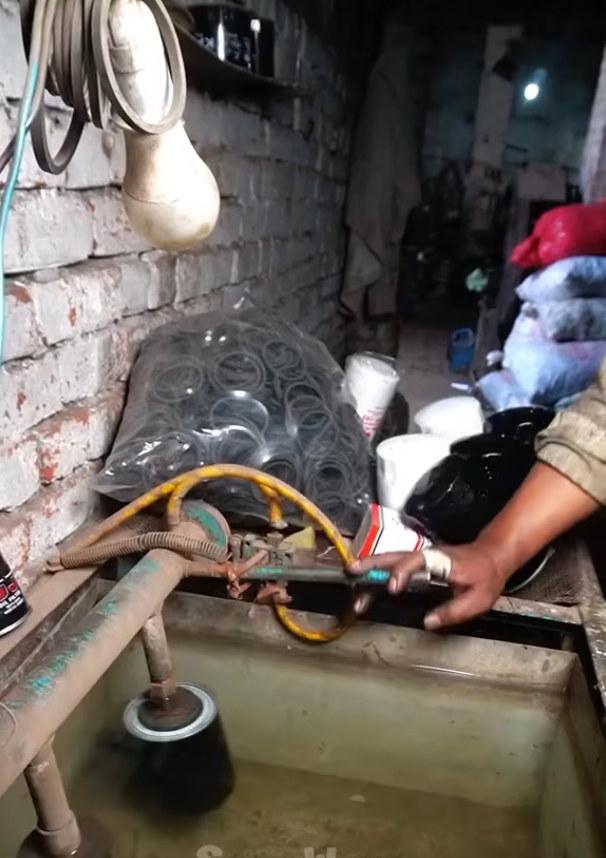
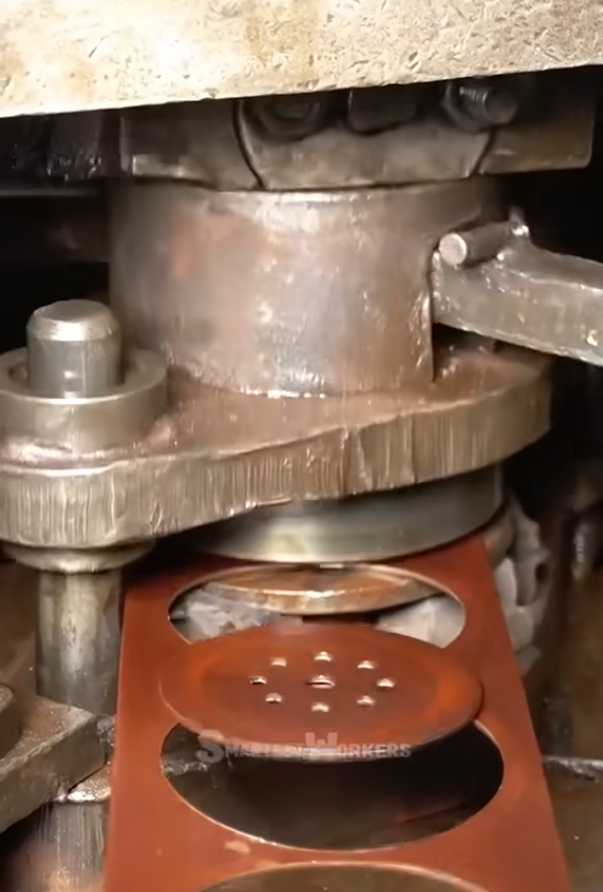
1. Designing the Oil Filter with Production in Mind
The initial design phase is crucial. Engineers need to consider:
- Filtration Material: Select a filter medium capable of capturing even the smallest particles (like cellulose or synthetic fibers). The material should withstand high temperatures and pressures.
- Housing Durability: The filter’s housing must be strong enough to endure engine vibrations and prevent leaks.
- Optimized Shape and Size: Ensuring the filter fits various engine types can make the filter versatile across vehicle models, reducing production complexity.
By addressing these considerations in the design phase, manufacturers can prevent production delays and quality control issues later on.
2. Automation and Robotics for Consistent Assembly
Consistency is essential in high-volume production. Automation plays a crucial role in:
- Material Handling: Robotic arms can handle delicate filter media, preventing damage and ensuring precise placement.
- Automated Cutting and Pleating: Pleating the filter media increases surface area, improving filtration efficiency. Automated pleating machines ensure uniformity across filters, critical for maintaining product standards.
- Assembly Line Optimization: Robotics can integrate various components (like the filter media, spring, and end cap) in quick succession, ensuring tightness and durability while minimizing human error.
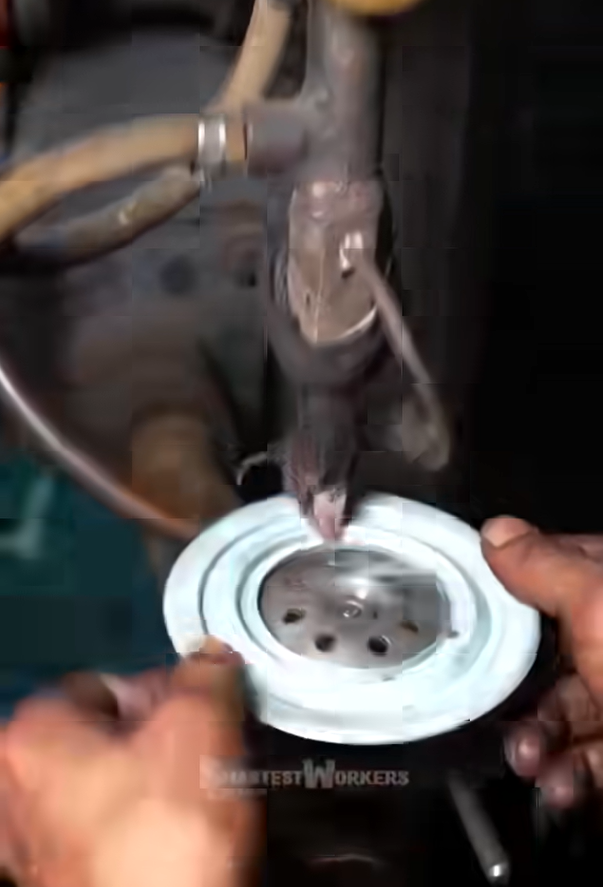
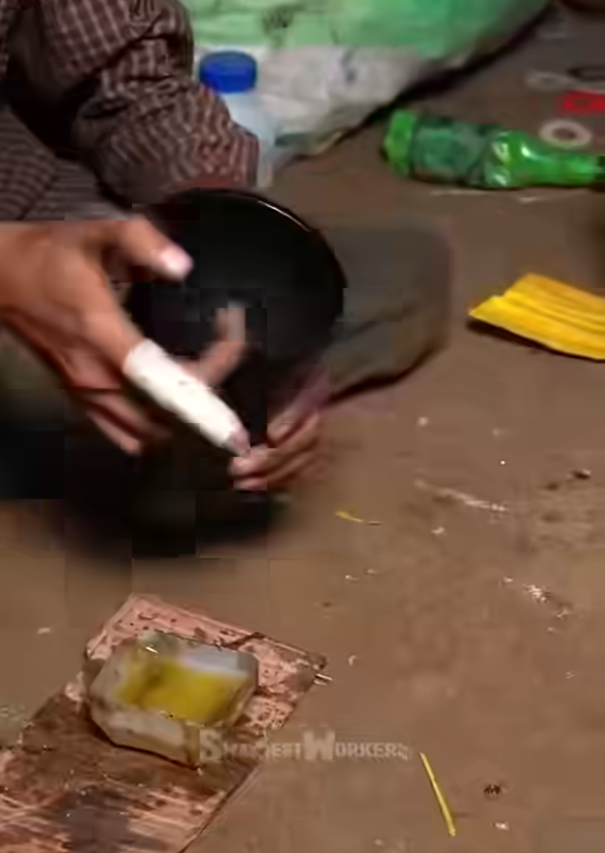
3. Advanced Quality Control Systems
Ensuring each oil filter meets stringent quality standards is a challenge at scale, but quality control (QC) methods have evolved to support mass production:
- Vision Systems: Cameras and sensors detect physical defects, such as missing parts or improper assembly, on the production line.
- Pressure and Leak Testing: Filters are tested under simulated engine conditions to ensure they can withstand high pressures and prevent leaks. Automated pressure testers allow rapid, consistent testing.
- Continuous Process Monitoring: Real-time data monitoring helps identify potential issues in material quality or assembly, allowing adjustments before they affect large production runs.
4. Efficient Supply Chain Management
Quality mass production relies on a steady supply of raw materials. A streamlined supply chain ensures consistency in the materials used for each filter.
- Strategic Sourcing: Working with trusted suppliers guarantees consistent raw material quality, while having backup suppliers prevents bottlenecks.
- Inventory Management: Real-time tracking and predictive analytics help forecast demand and manage inventory levels, avoiding delays due to material shortages.
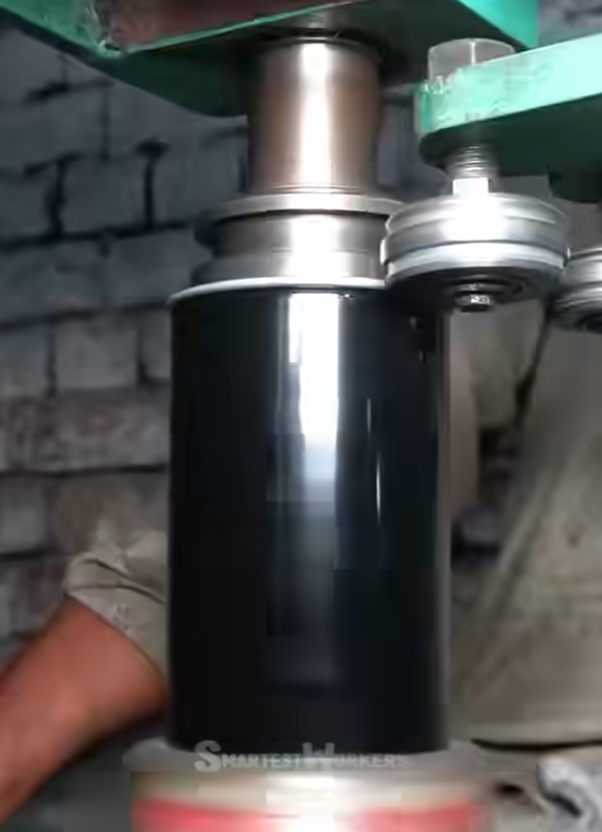
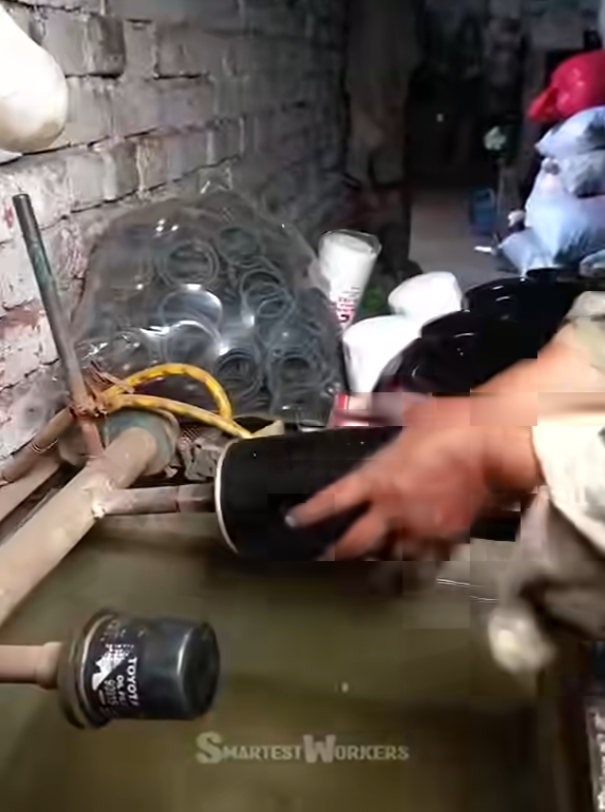
5. Lean Manufacturing Practices
Lean manufacturing is essential to minimize waste and maximize productivity:
- Just-In-Time (JIT) Production: Producing filters as they’re needed reduces inventory costs and increases responsiveness to demand changes.
- 5S System: By organizing the workspace efficiently, manufacturers can reduce downtime and improve productivity, allowing faster turnaround times for large orders.
- Continuous Improvement (Kaizen): Engaging employees in regular process improvements can help identify areas where quality and efficiency can be optimized without increasing costs.
6. Environmental and Regulatory Compliance
Sustainability is becoming increasingly important in manufacturing. Oil filter production can be resource-intensive, so manufacturers should consider:
- Eco-Friendly Materials: Some manufacturers are exploring biodegradable or recyclable materials for filter media and housing.
- Efficient Waste Management: Recycling filter materials, particularly metals, can reduce waste and meet environmental regulations.
- Adherence to Standards: Compliance with international standards, such as ISO 4548 for automotive filters, ensures that the final product meets performance and safety benchmarks.
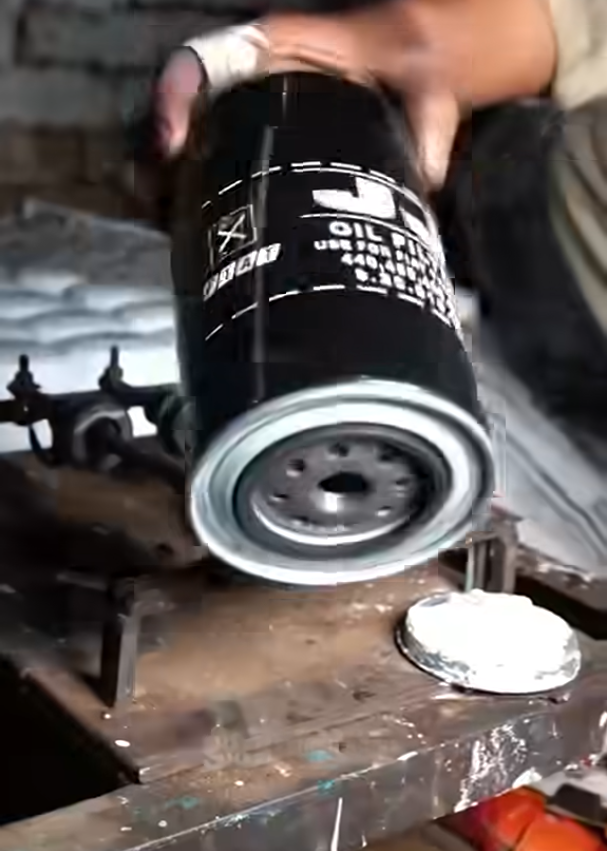
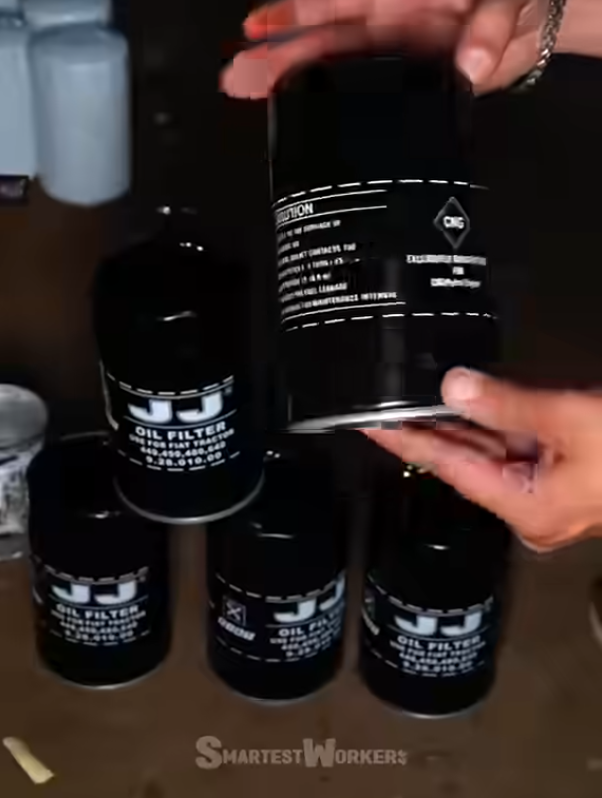
Conclusion
Producing high-quality engine oil filters at scale is achievable with careful planning, advanced technology, and a commitment to quality. From thoughtful design and automation to rigorous quality control, each step in the process contributes to a final product that can withstand the demands of modern engines. As manufacturers continue to innovate, the mass production of engine oil filters will become even more efficient and sustainable, supporting the automotive industry with reliable, high-performance filters for the engines of today and tomorrow.